Passenger & Goods Lift Inspections
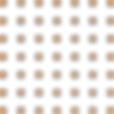
Lifts are a fundamental part of everyday movement within residential, commercial, and industrial settings. Whether transporting people or goods, these systems must operate safely and reliably - and that starts with regular inspections under LOLER and PUWER.
At Excel Inspection Solutions, we carry out statutory inspections on all types of vertical transportation equipment, from dumbwaiters and platform lifts to large passenger lifts in public and private buildings. We also offer in-depth maintenance audits and condition surveys to give you a full picture of your lift's performance and safety.
What types of lifts do we inspect?
Our team of qualified engineer surveyors inspect a wide range of lift equipment including:
-
Passenger lifts (commercial, residential, and public buildings)
-
Platform lifts and step lifts
-
Home lifts and domestic installations
-
Goods lifts and service lifts
-
Kitchen lifts and dumbwaiters
-
Evacuation and disabled access lifts
Inspections are carried out in accordance with LOLER (Lifting Operations and Lifting Equipment Regulations 1998) and, where relevant, PUWER.
LOLER for passenger and goods lifts
LOLER requires that all lifting equipment used to lift people is thoroughly examined at least every 6 months, and every 12 months for equipment lifting goods only.
As part of our LOLER service, we:
-
Conduct a full visual and functional inspection
-
Check lift components including safety gear, doors, controls, and alarm systems
-
Review previous reports and maintenance records
-
Highlight any defects that affect safety or compliance
-
Provide a digital LOLER report with photographic evidence
We also inspect associated equipment such as suspension chains, ropes, and lifting accessories.
Why regular inspection matters
Lifts that carry people or goods are subject to constant wear. Even minor faults can become major hazards if left unchecked. Regular inspections:
-
Ensure compliance with LOLER and PUWER
-
Help prevent breakdowns and expensive repairs
-
Reduce liability and risk to users
-
Support insurance and legal documentation
-
Maintain confidence in lift reliability and safety
Maintenance audits and condition surveys
Looking for a more detailed review of your lift performance? Our audits and condition surveys go beyond basic compliance. We provide:
-
Full system health checks
-
Analysis of usage, wear, and maintenance routines
-
Life expectancy estimates
-
Repair and upgrade recommendations
-
Support for budget planning and asset management
These services are ideal for property managers, housing associations, and facilities teams looking for proactive lift management.
Why choose Excel Inspection Solutions?
Our inspections are designed around your property type, lift usage, and legal duties. Whether it’s a home lift, platform lift, or commercial passenger system, we provide clear, compliant, and independent assessments.
-
Fully qualified LOLER and PUWER surveyors
-
Digital reporting with photographic evidence
-
Optional condition surveys and audits
-
Flexible scheduling and UK-wide coverage
-
Trusted by housing providers, councils, and FM companies
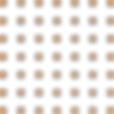
Passenger & Goods Lift – FAQs
How often does a passenger lift need to be inspected?
Under LOLER, lifts carrying people must be inspected at least every 6 months by a competent person.
Do I need LOLER inspections for a dumbwaiter?
Yes, if the dumbwaiter lifts goods and is used in a workplace setting. The inspection frequency is typically every 12 months.
Can you inspect lifts in private homes?
Yes. We inspect home lifts and domestic platform lifts to ensure they remain safe and compliant.
What is a lift condition survey?
It’s a detailed assessment of a lift’s condition, identifying wear, expected lifespan, and any maintenance or upgrade needs.
What happens if a lift fails its inspection?
We’ll issue a report highlighting defects and recommend that the lift is taken out of service until rectified. We can also advise on next steps.